Production
Throughout 6 generations, Alland & Robert has acquired a strong expertise regarding the production of natural gums.
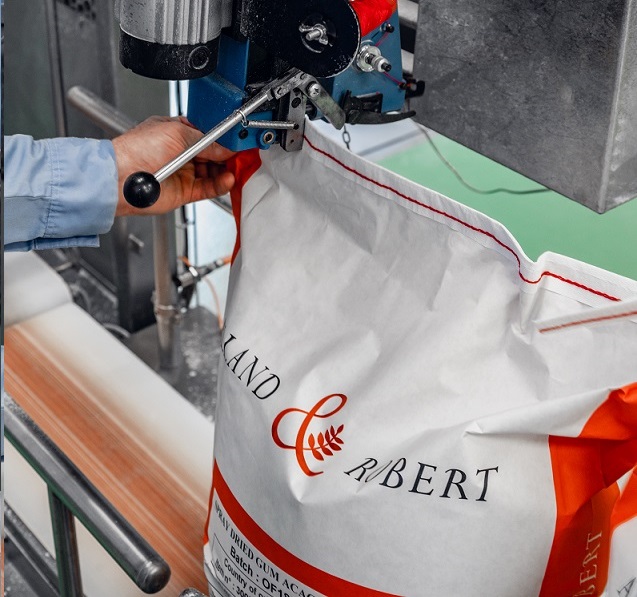
A sophisticated supply chain
Alland & Robert has acquired a strong expertise regarding the production of acacia gum and karaya gum, and has improved the production lines and work safety a lot over the years. The production process has also evolved to allow Alland & Robert to manufacture tailor-made products that follow customers strict specifications, and to develop products dedicated to certain functional properties or specific applications.
Every year, Alland & Robert is investing to improve the process and respect the environment.
Spray drying acacia gum
Alland & Robert has built 3 spray drying towers, respectively in 2002, 2007 and 2013. This highly technical equipment provides production of instant soluble and spray dried grades of acacia gum.
We make every effort to provide customers with a safe, healthy products, and take the environmental and quality aspects into consideration at every stage of the production process.
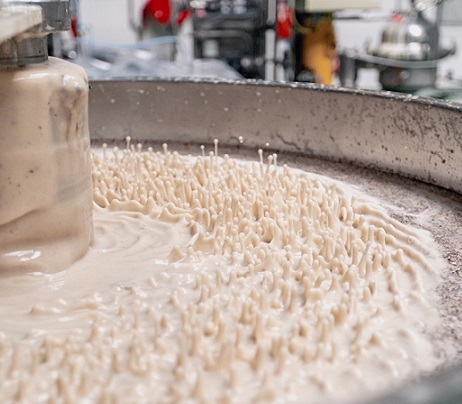